Mechanikus tömítéseknagyon fontos szerepet játszanak a szivárgás elkerülésében számos különböző iparágban. A tengerészeti iparban vannakszivattyú mechanikus tömítések, forgótengelyes mechanikus tömítések. Az olaj- és gáziparban pedig vannakpatronos mechanikus tömítések,osztott mechanikus tömítések vagy száraz gáz mechanikus tömítések. Az autóiparban víz mechanikus tömítések léteznek. A vegyiparban pedig keverő mechanikus tömítések (keverőgép mechanikus tömítések) és kompresszor mechanikus tömítések.
A különböző felhasználási körülményektől függően különböző anyagú mechanikus tömítőoldatokra van szükség. Sokféle anyagot használnak a...mechanikus tengelytömítések például kerámia mechanikus tömítések, szén mechanikus tömítések, szilikon-karbid mechanikus tömítések,SSIC mechanikus tömítések ésTC mechanikus tömítések.
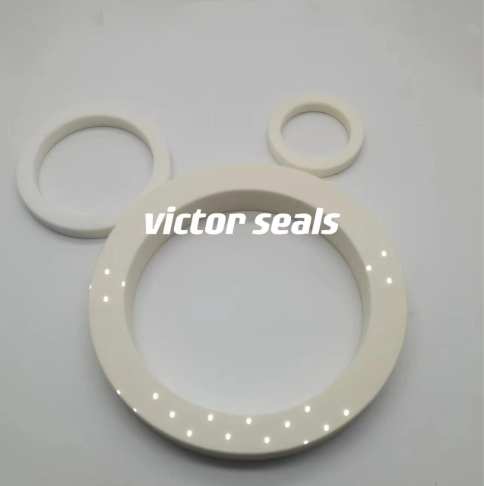
Kerámia mechanikus tömítések
A kerámia mechanikus tömítések kritikus alkatrészek különféle ipari alkalmazásokban, amelyeket úgy terveztek, hogy megakadályozzák a folyadékok szivárgását két felület, például egy forgó tengely és egy álló ház között. Ezeket a tömítéseket nagyra értékelik kivételes kopásállóságuk, korrózióállóságuk és szélsőséges hőmérsékleteknek való ellenállásuk miatt.
A kerámia mechanikus tömítések elsődleges szerepe a berendezések integritásának fenntartása a folyadékveszteség vagy szennyeződés megakadályozásával. Számos iparágban használják őket, beleértve az olaj- és gázipart, a vegyipari feldolgozást, a vízkezelést, a gyógyszeripart és az élelmiszer-feldolgozást. Ezen tömítések széles körű elterjedése tartós konstrukciójuknak tudható be; fejlett kerámia anyagokból készülnek, amelyek kiváló teljesítményjellemzőket kínálnak más tömítőanyagokhoz képest.
A kerámia mechanikus tömítések két fő alkotóelemből állnak: az egyik egy mechanikus állófelület (általában kerámia anyagból készül), a másik pedig egy mechanikus forgófelület (általában széngrafitból készül). A tömítőhatás akkor következik be, amikor a két felületet rugóerővel összenyomják, ami hatékony gátat hoz létre a folyadékszivárgás ellen. A berendezés működése közben a tömítőfelületek közötti kenőfilm csökkenti a súrlódást és a kopást, miközben szoros tömítést biztosít.
Az egyik kulcsfontosságú tényező, amely megkülönbözteti a kerámia mechanikus tömítéseket más típusoktól, a kiemelkedő kopásállóságuk. A kerámia anyagok kiváló keménységi tulajdonságokkal rendelkeznek, amelyek lehetővé teszik számukra, hogy jelentős károsodás nélkül bírják az abrazív körülményeket. Ez hosszabb élettartamú tömítéseket eredményez, amelyek ritkább cserét vagy karbantartást igényelnek, mint a puhább anyagokból készült tömítések.
A kopásállóság mellett a kerámiák kivételes hőstabilitást is mutatnak. Magas hőmérsékletet is elviselnek anélkül, hogy degradációt szenvednének, vagy elveszítenék tömítőképességüket. Ez alkalmassá teszi őket magas hőmérsékletű alkalmazásokban való használatra, ahol más tömítőanyagok idő előtt meghibásodhatnak.
Végül, a kerámia mechanikus tömítések kiváló kémiai kompatibilitást kínálnak, és ellenállnak a különféle korrozív anyagoknak. Ez vonzó választássá teszi őket azoknak az iparágaknak, amelyek rendszeresen dolgoznak agresszív vegyszerekkel és folyadékokkal.
A kerámia mechanikus tömítések elengedhetetlenekalkatrésztömítésekÚgy tervezték, hogy megakadályozzák a folyadék szivárgását ipari berendezésekben. Egyedülálló tulajdonságaik, mint például a kopásállóság, a hőstabilitás és a kémiai kompatibilitás, előnyben részesítik őket különféle alkalmazásokhoz számos iparágban.
kerámia fizikai tulajdonság | ||||
Műszaki paraméter | egység | 95% | 99% | 99,50% |
Sűrűség | g/cm3 | 3.7 | 3.88 | 3.9 |
Keménység | HRA | 85 | 88 | 90 |
Porozitási arány | % | 0,4 | 0,2 | 0,15 |
Törési szilárdság | MPa | 250 | 310 | 350 |
Hőtágulási együttható | 10(-6)/Ó | 5.5 | 5.3 | 5.2 |
Hővezető képesség | W/MK | 27.8 | 26.7 | 26 |
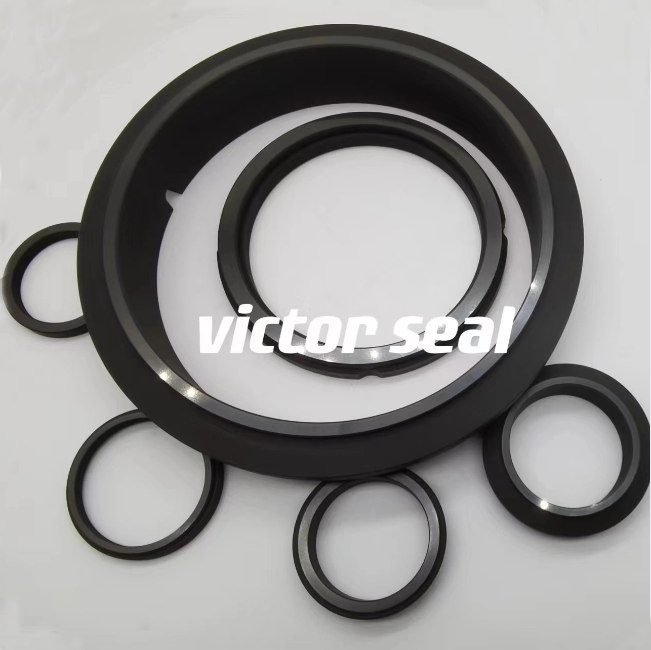
Szén mechanikus tömítések
A mechanikus széntömítéseknek hosszú története van. A grafit a szén egyik izoformája. 1971-ben az Egyesült Államokban sikeresen tanulmányozták a rugalmas grafit mechanikus tömítőanyagot, amely megoldotta az atomenergia-szelepek szivárgásának problémáját. A mélyreható feldolgozás után a rugalmas grafit kiváló tömítőanyaggá válik, amelyből különféle szén mechanikus tömítéseket készítenek, tömítőelemekként. Ezeket a szén mechanikus tömítéseket a vegyiparban, a kőolajiparban és az elektromos energiaiparban használják, például magas hőmérsékletű folyadéktömítésként.
Mivel a rugalmas grafit a magas hőmérséklet hatására expandált grafit tágulása révén képződik, a rugalmas grafitban maradó interkalációs szer mennyisége nagyon kicsi, de nem teljesen, így az interkalációs szer megléte és összetétele nagyban befolyásolja a termék minőségét és teljesítményét.
Szén tömítőfelület anyagának kiválasztása
Az eredeti feltaláló tömény kénsavat használt oxidálószerként és interkalálószerként. Azonban miután egy fém alkatrész tömítésére felvitték, a rugalmas grafitban maradt kis mennyiségű kén hosszú távú használat után korrodálta az érintkező fémet. Ennek fényében néhány hazai tudós megpróbálta javítani, például Song Kemin, aki ecetsavat és szerves savat választott a kénsav helyett. Salétromsav, lassú hatóidejű salétromsav, szobahőmérsékletűre csökkentve, salétromsav és ecetsav keverékéből készült. Salétromsav és ecetsav keverékének felhasználásával kénmentes expandált grafitot készítettek kálium-permanganáttal oxidálószerként, és ecetsavat lassan adagoltak a salétromsavhoz. A hőmérsékletet szobahőmérsékletre csökkentették, és elkészítették a salétromsav és ecetsav keverékét. Ezután a természetes pehelygrafitot és a kálium-permanganátot adták ehhez a keverékhez. Állandó keverés mellett a hőmérséklet 30 °C volt. 40 perces reakcióidő után a vizet semlegesre mossák, 50-60 °C-on szárítják, és magas hőmérsékletű expandált grafitot készítettek. Ez a módszer nem eredményez vulkanizálást, feltéve, hogy a termék elér egy bizonyos térfogatnyi tágulást, így a tömítőanyag viszonylag stabil jelleget biztosít.
Típus | M106H | M120H | M106K | M120K | M106F | M120F | M106D | M120D | M254D |
Márka | Impregnált | Impregnált | Impregnált fenol | Antimon Szén(A) | |||||
Sűrűség | 1,75 | 1.7 | 1,75 | 1.7 | 1,75 | 1.7 | 2.3 | 2.3 | 2.3 |
Törési szilárdság | 65 | 60 | 67 | 62 | 60 | 55 | 65 | 60 | 55 |
Nyomószilárdság | 200 | 180 | 200 | 180 | 200 | 180 | 220 | 220 | 210 |
Keménység | 85 | 80 | 90 | 85 | 85 | 80 | 90 | 90 | 65 |
Porozitás | <1 | <1 | <1 | <1 | <1 | <1 | <1,5 | <1,5 | <1,5 |
Hőmérsékletek | 250 | 250 | 250 | 250 | 250 | 250 | 400 | 400 | 450 |
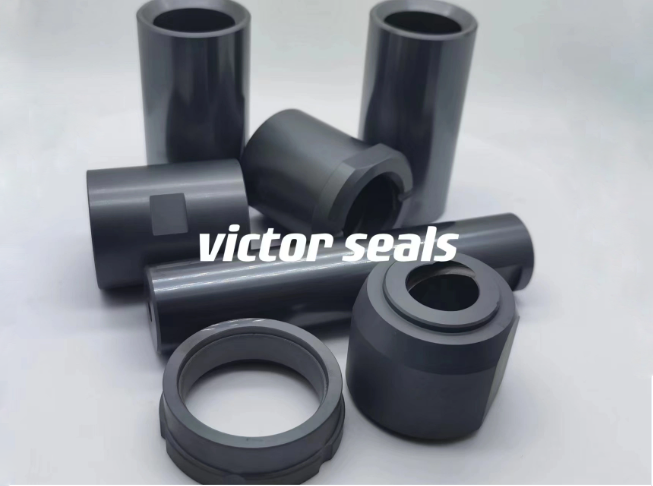
Szilícium-karbid mechanikus tömítések
A szilícium-karbid (SiC) karborundum néven is ismert, és kvarchomokból, petróleumkokszból (vagy szénkokszból), faforgácsból (amelyet a zöld szilícium-karbid előállításánál kell hozzáadni) stb. készül. A szilícium-karbidnak van egy ritka ásványa is a természetben, az eperfa. A kortárs C, N, B és más nemoxidos, csúcstechnológiás tűzálló alapanyagokban a szilícium-karbid az egyik legszélesebb körben használt és leggazdaságosabb anyag, amelyet aranyacél homoknak vagy tűzálló homoknak is nevezhetünk. Jelenleg Kína ipari szilícium-karbid termelése fekete szilícium-karbidra és zöld szilícium-karbidra oszlik, mindkettő hatszögletű kristály, 3,20 ~ 3,25 arányban és 2840 ~ 3320 kg/m² mikrokeménységgel.
A szilícium-karbid termékeket a különböző alkalmazási környezetek szerint sokféle típusba sorolják. Általában mechanikailag használják. Például a szilícium-karbid ideális anyag a szilícium-karbid mechanikus tömítésekhez, mivel jó kémiai korrózióállósággal, nagy szilárdsággal, nagy keménységgel, jó kopásállósággal, kis súrlódási együtthatóval és magas hőmérséklettel szembeni ellenállással rendelkezik.
A SIC tömítőgyűrűk statikus gyűrűkre, mozgó gyűrűkre, lapos gyűrűkre és így tovább oszthatók. A SiC szilíciumból különféle keményfém termékek készülhetnek, például szilícium-karbid forgógyűrű, szilícium-karbid álló szelepülés, szilícium-karbid persely stb., az ügyfelek speciális igényei szerint. Grafit anyaggal kombinálva is használható, és súrlódási együtthatója kisebb, mint az alumínium-oxid kerámiáé és a kemény ötvözeté, így nagy fotovoltaikus értékek esetén használható, különösen erős savak és erős lúgok között.
A SIC csökkentett súrlódása az egyik legfontosabb előnye a mechanikus tömítésekben való alkalmazásának. A SIC ezért jobban ellenáll a kopásnak és elhasználódásnak, mint más anyagok, meghosszabbítva a tömítés élettartamát. Ezenkívül a SIC csökkent súrlódása csökkenti a kenés szükségességét. A kenés hiánya csökkenti a szennyeződés és a korrózió lehetőségét, javítva a hatékonyságot és a megbízhatóságot.
A SIC kiváló kopásállósággal is rendelkezik. Ez azt jelzi, hogy folyamatos használatot is kibír anélkül, hogy romlana vagy szakadna. Ezáltal tökéletes anyag olyan felhasználási területekre, amelyek nagyfokú megbízhatóságot és tartósságot igényelnek.
Újracsiszolható és polírozható, így a tömítés élettartama alatt többször is felújítható. Általában mechanikaibb célokra használják, például mechanikus tömítésekben, jó kémiai korrózióállósága, nagy szilárdsága, nagy keménysége, jó kopásállósága, kis súrlódási együtthatója és magas hőmérsékletállósága miatt.
Mechanikus tömítőfelületekhez használva a szilícium-karbid jobb teljesítményt, hosszabb tömítési élettartamot, alacsonyabb karbantartási költségeket és alacsonyabb üzemeltetési költségeket eredményez a forgó berendezések, például turbinák, kompresszorok és centrifugálszivattyúk esetében. A szilícium-karbid tulajdonságai a gyártási módjától függően eltérőek lehetnek. A reakciókötésű szilícium-karbidot a szilícium-karbid részecskék reakciófolyamatban történő egymáshoz kötésével állítják elő.
Ez az eljárás nem befolyásolja jelentősen az anyag fizikai és termikus tulajdonságainak nagy részét, azonban korlátozza az anyag kémiai ellenálló képességét. A leggyakoribb problémát jelentő vegyi anyagok a lúgok (és más magas pH-értékű vegyi anyagok) és az erős savak, ezért a reakciókötésű szilícium-karbidot nem szabad ezekben az alkalmazásokban használni.
Reakciós szinterezett, infiltráltszilícium-karbid. Az ilyen anyagban az eredeti SIC anyag pórusai a fémes szilícium kiégetésével töltődnek be az infiltráció során, így másodlagos SiC jelenik meg, és az anyag kivételes mechanikai tulajdonságokra tesz szert, kopásállóvá válik. Minimális zsugorodása miatt nagy és összetett alkatrészek gyártásában használható szűk tűréshatárokkal. A szilíciumtartalom azonban a maximális üzemi hőmérsékletet 1350 °C-ra korlátozza, a kémiai ellenállás is körülbelül pH 10-re korlátozódik. Az anyag nem ajánlott agresszív lúgos környezetben való használatra.
SzinterezettA szilícium-karbidot úgy állítják elő, hogy egy előpréselt, nagyon finom SIC-granulátumot 2000 °C-on szintereznek, így erős kötések alakulnak ki az anyag szemcséi között.
Először a rács vastagszik, majd csökken a porozitás, végül a szemcsék közötti kötések szintereződnek. Az ilyen feldolgozás során a termék jelentős – körülbelül 20%-os – zsugorodása következik be.
SSIC tömítőgyűrű minden vegyszerrel szemben ellenálló. Mivel szerkezetében nincs fémes szilícium, akár 1600 °C-os hőmérsékleten is használható anélkül, hogy ez befolyásolná a szilárdságát.
ingatlanok | R-SiC | S-SiC |
Porozitás (%) | ≤0,3 | ≤0,2 |
Sűrűség (g/cm3) | 3.05 | 3,1~3,15 |
Keménység | 110~125 (HS) | 2800 (kg/mm2) |
Rugalmassági modulus (Gpa) | ≥400 | ≥410 |
SiC-tartalom (%) | ≥85% | ≥99% |
Si-tartalom (%) | ≤15% | 0,10% |
Hajlítószilárdság (MPa) | ≥350 | 450 |
Nyomószilárdság (kg/mm2) | ≥2200 | 3900 |
Hőtágulási együttható (1/℃) | 4,5 × 10⁻⁶ | 4,3×10⁻⁶ |
Hőállóság (atmoszférában) (℃) | 1300 | 1600 |
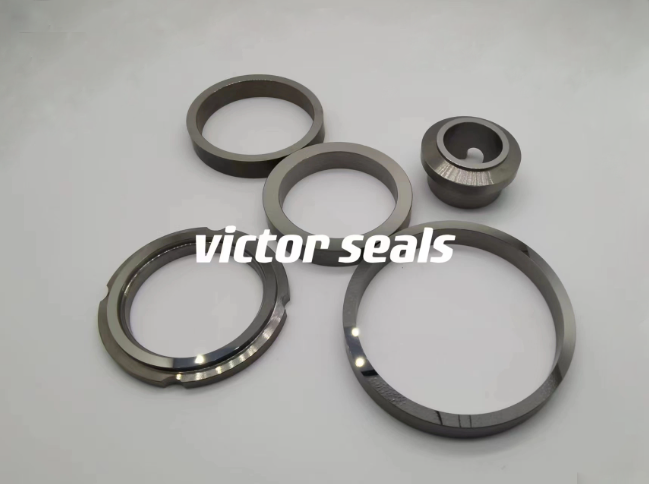
TC mechanikus tömítés
A TC anyagok nagy keménységgel, szilárdsággal, kopásállósággal és korrózióállósággal rendelkeznek. „Ipari fogként” is ismertek. Kiváló teljesítményének köszönhetően széles körben használják a hadiiparban, a repülőgépiparban, a gépiparban, a kohászatban, az olajfúrásban, az elektronikus kommunikációban, az építészetben és más területeken. Például szivattyúkban, kompresszorokban és keverőkben a volfrám-karbid gyűrűket mechanikus tömítésként használják. A jó kopásállóság és a nagy keménység alkalmassá teszi őket a magas hőmérsékletnek, súrlódásnak és korróziónak kitett kopásálló alkatrészek gyártására.
Kémiai összetétele és felhasználási jellemzői szerint a TC négy kategóriába sorolható: volfrám-kobalt (YG), volfrám-titán (YT), volfrám-titán-tantál (YW) és titán-karbid (YN).
A volfrám-kobalt (YG) keményötvözet WC-ből és Co-ból áll. Alkalmas rideg anyagok, például öntöttvas, színesfémek és nemfémes anyagok megmunkálására.
A sztellit (YT) WC-ből, TiC-ből és Co-ból áll. A TiC hozzáadása az ötvözethez javítja a kopásállóságát, de csökkenti a hajlítószilárdságát, a csiszolási teljesítményét és a hővezető képességét. Alacsony hőmérsékleten mutatott ridegsége miatt csak általános anyagok nagysebességű forgácsolására alkalmas, rideg anyagok megmunkálására nem.
A volfrám-titán-tantál (nióbium)-kobaltot (YW) adnak az ötvözethez a magas hőmérsékletű keménység, szilárdság és kopásállóság növelése érdekében megfelelő mennyiségű tantál-karbid vagy nióbium-karbid hozzáadásával. Ugyanakkor a szívósság is javul, és jobb átfogó vágási teljesítményt nyújt. Főleg kemény forgácsolható anyagokhoz és szakaszos forgácsoláshoz használják.
A karbonizált titán alaposztály (YN) egy kemény ötvözet, amely TiC, nikkel és molibdén kemény fázisát tartalmazza. Előnyei a nagy keménység, a kötésállóság, a félholdkopás-gátlás és az oxidációgátlás. 1000 fok feletti hőmérsékleten is megmunkálható. Alkalmazható ötvözött acélok folyamatos simítására és edzéses acélok gyártására.
modell | nikkeltartalom (tömeg%) | sűrűség (g/cm²) | keménység (HRA) | hajlítószilárdság (≥N/mm²) |
YN6 | 5,7–6,2 | 14,5-14,9 | 88,5-91,0 | 1800 |
YN8 | 7,7–8,2 | 14,4-14,8 | 87,5-90,0 | 2000 |
modell | kobalttartalom (tömeg%) | sűrűség (g/cm²) | keménység (HRA) | hajlítószilárdság (≥N/mm²) |
YG6 | 5,8–6,2 | 14,6-15,0 | 89,5-91,0 | 1800 |
YG8 | 7,8-8,2 | 14,5-14,9 | 88,0–90,5 | 1980 |
YG12 | 11,7–12,2 | 13,9-14,5 | 87,5-89,5 | 2400 |
YG15 | 14,6–15,2 | 13,9–14,2 | 87,5-89,0 | 2480 |
YG20 | 19,6–20,2 | 13,4-13,7 | 85,5-88,0 | 2650 |
YG25 | 24,5-25,2 | 12,9–13,2 | 84,5-87,5 | 2850 |